
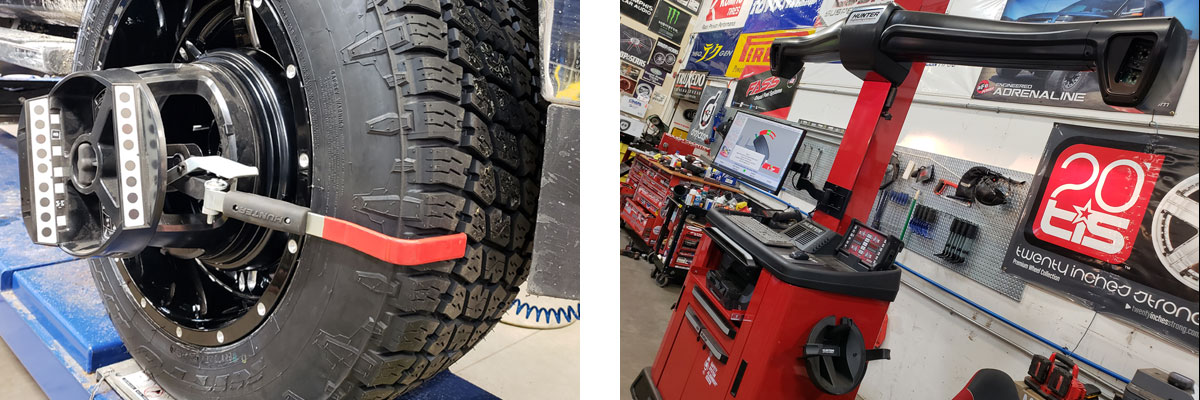
Instead of merely signalling that a problem is already occurring, periodically checking the state of your alignment may allow you to anticipate or even avert the need for major repairs. While keeping an eye on vibration levels is one well-established way to monitor the health of rotating machines, capture and analysis of actual alignment data will take your understanding and preparedness to the next level. Knowing the condition of your machines can help avoid or mitigate costly breakdowns and failures. 3: Trend diagram showing seasonal temperature changes and impact on the alignment condition Monitoring Machine Health As the outside temperatures changed with the seasons, a corresponding misalignment of the pump and pipe assembly became readily apparent.įig. The reason for misalignment was easy to identify when examining the trends in the coupling clearances. In the western American desert, summer heat often runs above 110° F (43° C), while in the winter temperatures sometimes fall below 0° F (-18° C). Trend charts revealed that seasonal temperature extremes were negatively affecting alignment. Again, vibration analysis exposed the misalignment, but it was analysis of alignment trends that identified the source of the problem. In this case, a pump and pipe assembly, which had been properly installed and aligned, was inexplicably running in and out of alignment. Maybe it’s a Weather ProblemĬapture and analysis of alignment trends also assisted in correcting pump alignment problems in a high desert environment.
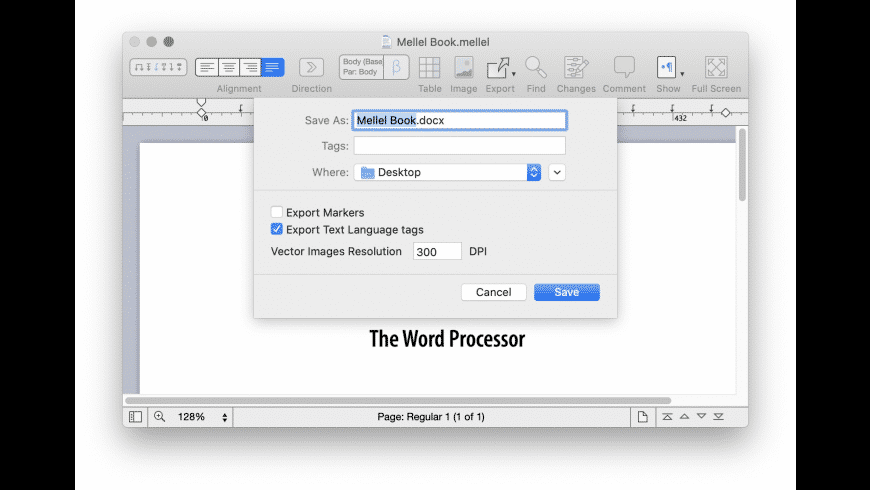
Vibration analysis had identified the misalignment problem, but only analysis of the gap and offset alignment trends revealed the reason why. By analyzing the alignment trends over time, it was discovered that the turbine foundation, built on fill dirt in an area of land recovered from San Francisco Bay, was slowly sinking. The requirement was always the same, the turbine needed to be shimmed up another 0.05-0.1 mm. In this real life example, a plant operator found that his machines needed realignment every six months. 2: Measurement results showing machine misalignment Maybe it’s a Foundation ProblemĬapture and analysis of alignment data trends proved useful at a co-generation plant in the San Francisco area. Periodically checking and recording alignment conditions generates useful information about correctable conditions that, if addressed, will reduce breakdowns, increase productivity, and save money.įig. Capturing alignment data before equipment is removed or disassembled, even when maintenance is undertaken for non-alignment reasons, may, over time, reveal hidden causes of misalignment. Vibration analysis might uncover a misalignment problem, but it won’t necessarily identify the reason for it. The root cause of a misalignment condition is not always obvious.
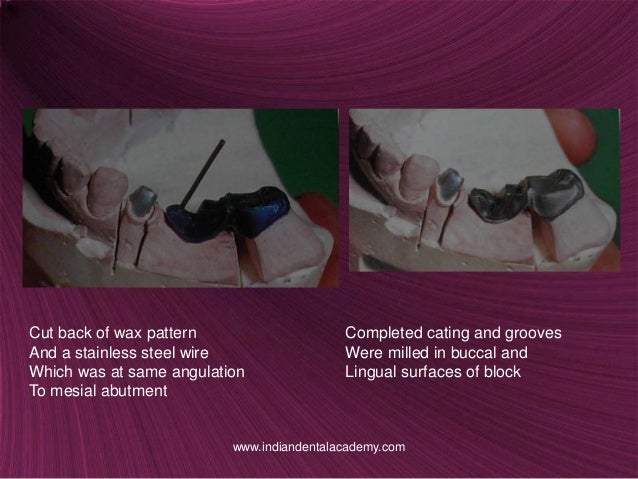
It Can Be Difficult to Identify the Cause of Misalignment
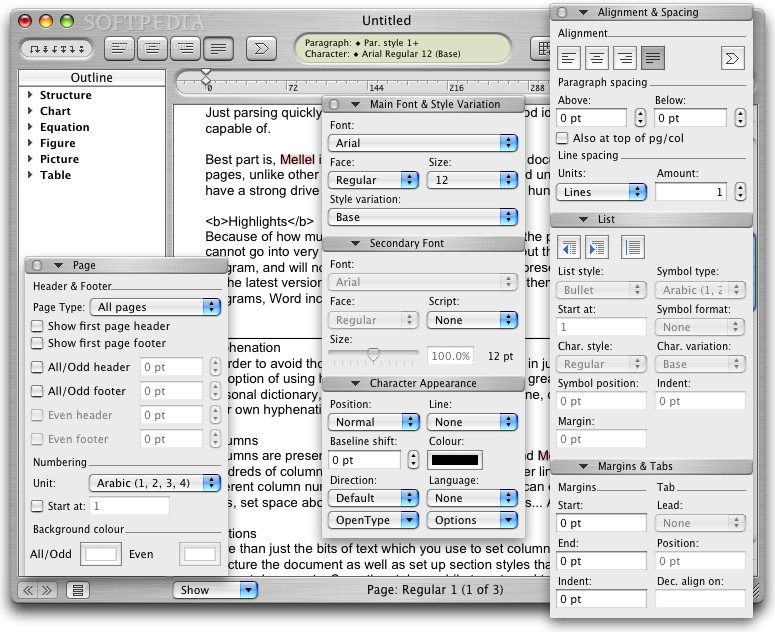
It depends on accurate and careful analysis of the trends in your alignment data. Effectively countering the factors that influence or alter alignment depends on understanding how the alignment of your machine changes over time and with use. Even the simple and natural succession of the seasons can alter alignment and put machine assets at risk. When minor process parameters such as pressure or temperature are modified, alignment can change. When a machine vibrates, its skids can move and affect its alignment. Alignment changes when a machine warms up, its alignment can shift with the thermal expansion of its parts. Fig.1: Over 50% of machine failures are due to misalignment
